Gas detection is a crucial aspect of ensuring safety in domestic and industrial environments. Two of the most common technologies used in gas detectors are infrared and catalytic sensors. Each of these technologies has specific advantages. In this article, we will take a detailed look at the features, pros and cons of both technologies to help understand which may be the best choice for different applications.
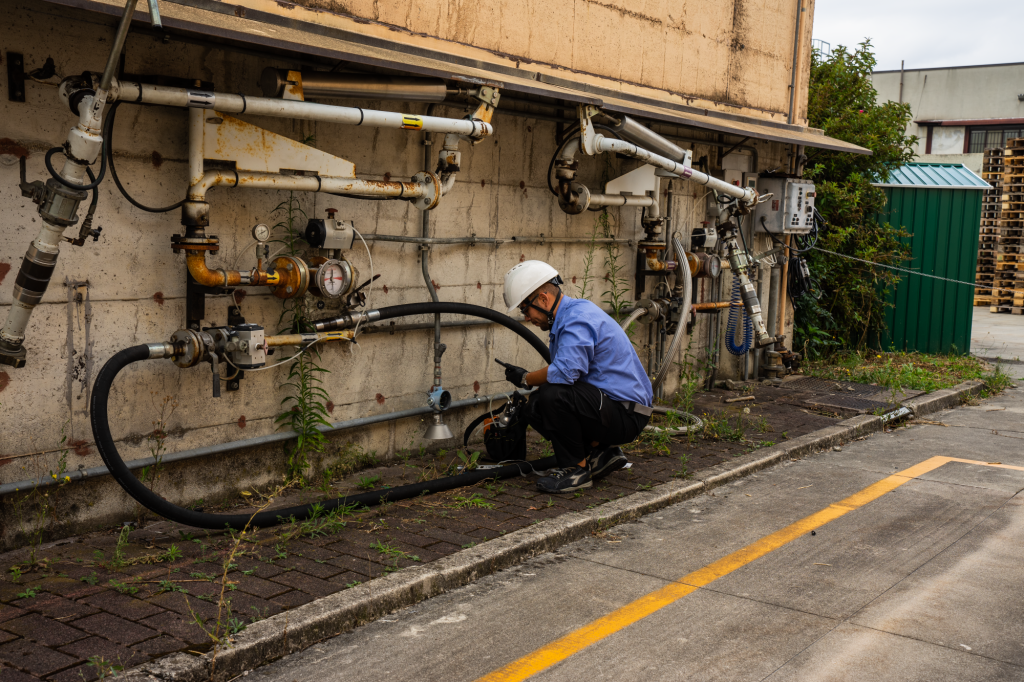
Gas detection: infrared sensors
Infrared (IR) sensors detect the presence of gas by measuring
the absorption of infrared light by gas molecules. An infrared light emitter sends a beam of light through the gas sample and a detector measures the intensity of the transmitted light. The amount of light absorbed is proportional to the concentration of gas present.
Sensors with infrared technology have several advantages:
- Accuracy and Reliability: Infrared sensors offer very accurate and reliable detection, with a low probability of false alarms.
- Long Life: These sensors have a long life, often longer than catalytic sensors, because they are not consumed by the detected gas.
- Oxygen-free: IR sensors can operate effectively in oxygen-free environments, making them ideal for indoor or underground applications.
- Low Maintenance: They require little maintenance compared to catalytic sensors, reducing long-term operating costs.
Gas detection: catalytic sensors
Catalytic sensors detect the presence of combustible gases by means of a catalytic reaction. The sensor contains a small heated element covered by a catalyst. When the gas comes into contact with the element, it oxidises, generating heat. The increase in temperature causes a change in the electrical resistance of the element, which is measured to determine the gas concentration.
Catalytic sensors have several advantages:
- Lower Cost: Catalytic sensors are generally cheaper to produce and purchase than infrared sensors.
- Wide Range of Detectable Gases: They can detect a wide range of combustible gases, including methane, propane and hydrogen.
- Reliability in Various Conditions: They work well in a variety of environmental conditions and can be used in many industrial applications.
Entrust the calibration and periodic maintenance of your gas detection systems to Sensitron
Our gas detection systems have different maintenance requirements depending on the gases detected and the applications in which they are used. Scheduled maintenance ensures the efficiency of gas detection systems with the resulting safety of workers and environments.
Entrusting periodic maintenance to our team means extending the life cycle of the instruments with an impact on both running costs and the environment.
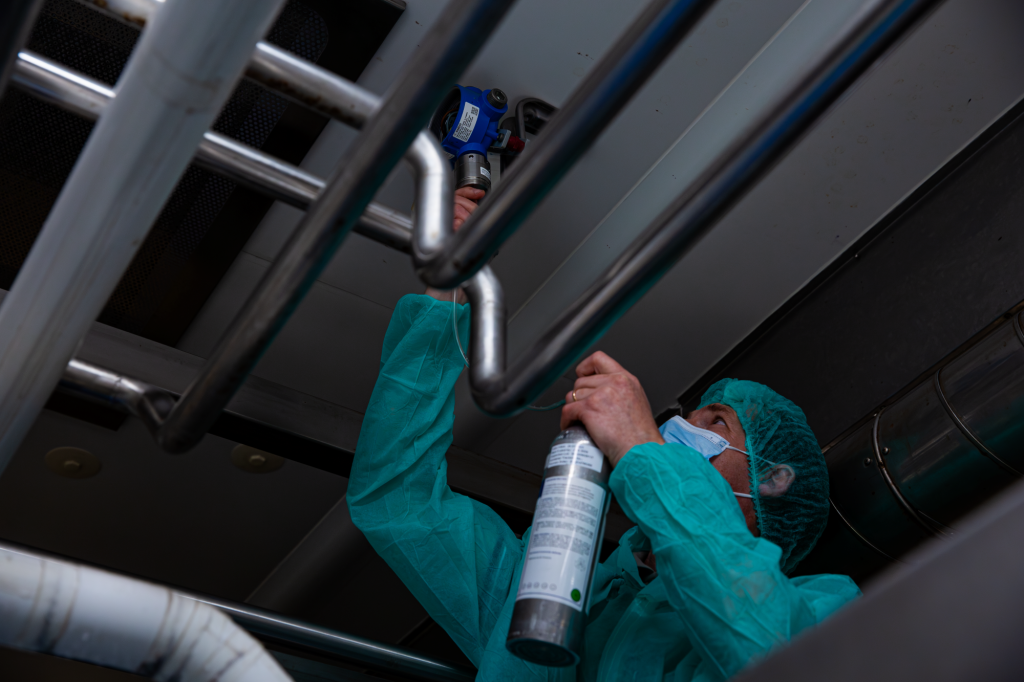
Discover our produtcs
Sensitron gas detection systems are suitable for use in any application:
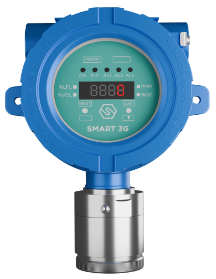
SMART 3G D2
Suitable for detecting flammable substances, toxic gases, refrigerants and oxygen in classified areas.ATEX, IECEx and SIL2/3 certified.
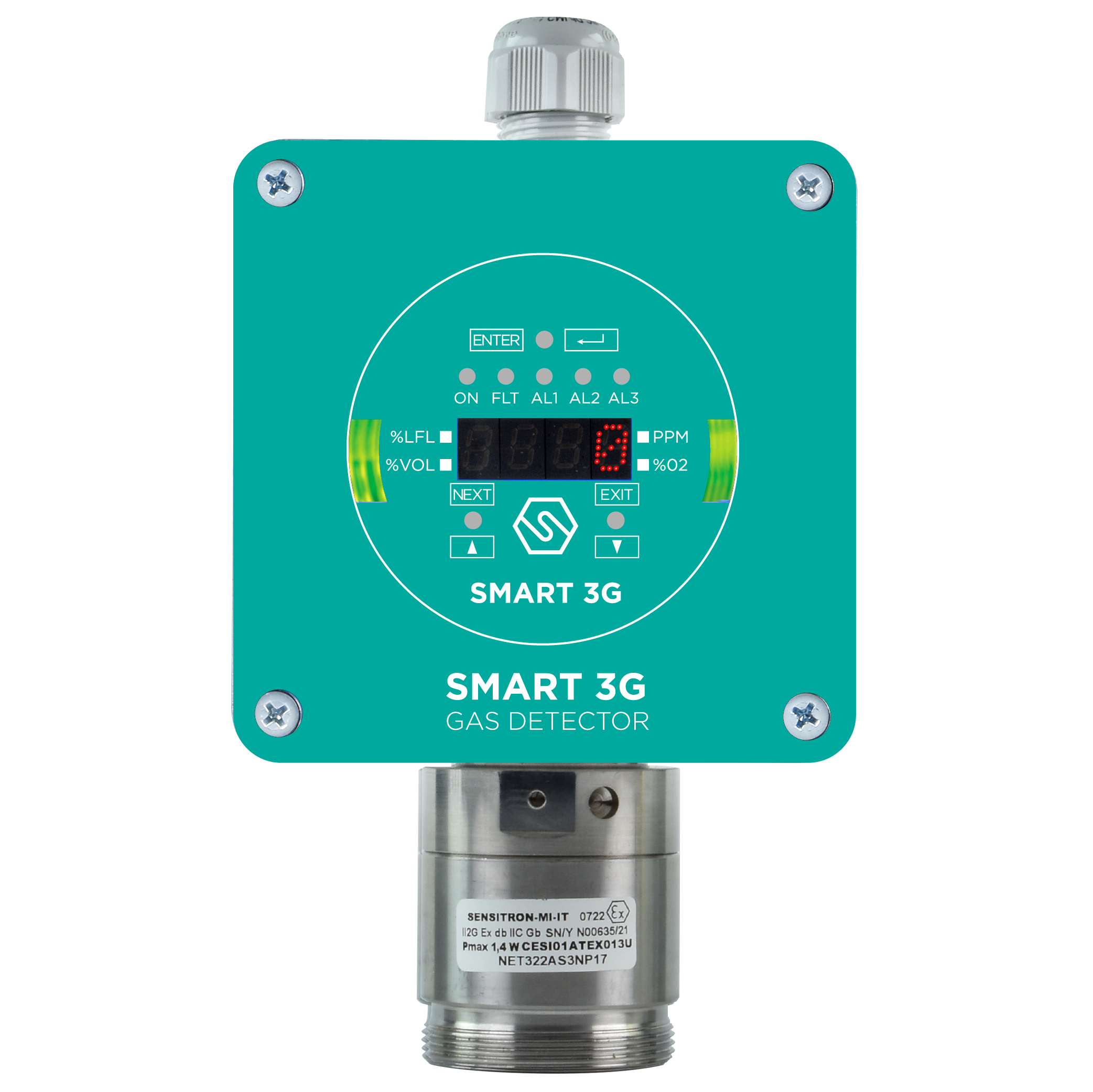
SMART 3G D3
Suitable for gas detection in classified areas, ATEX, IECEx and SIL2/3 certified, allows for non-intrusive field calibration.
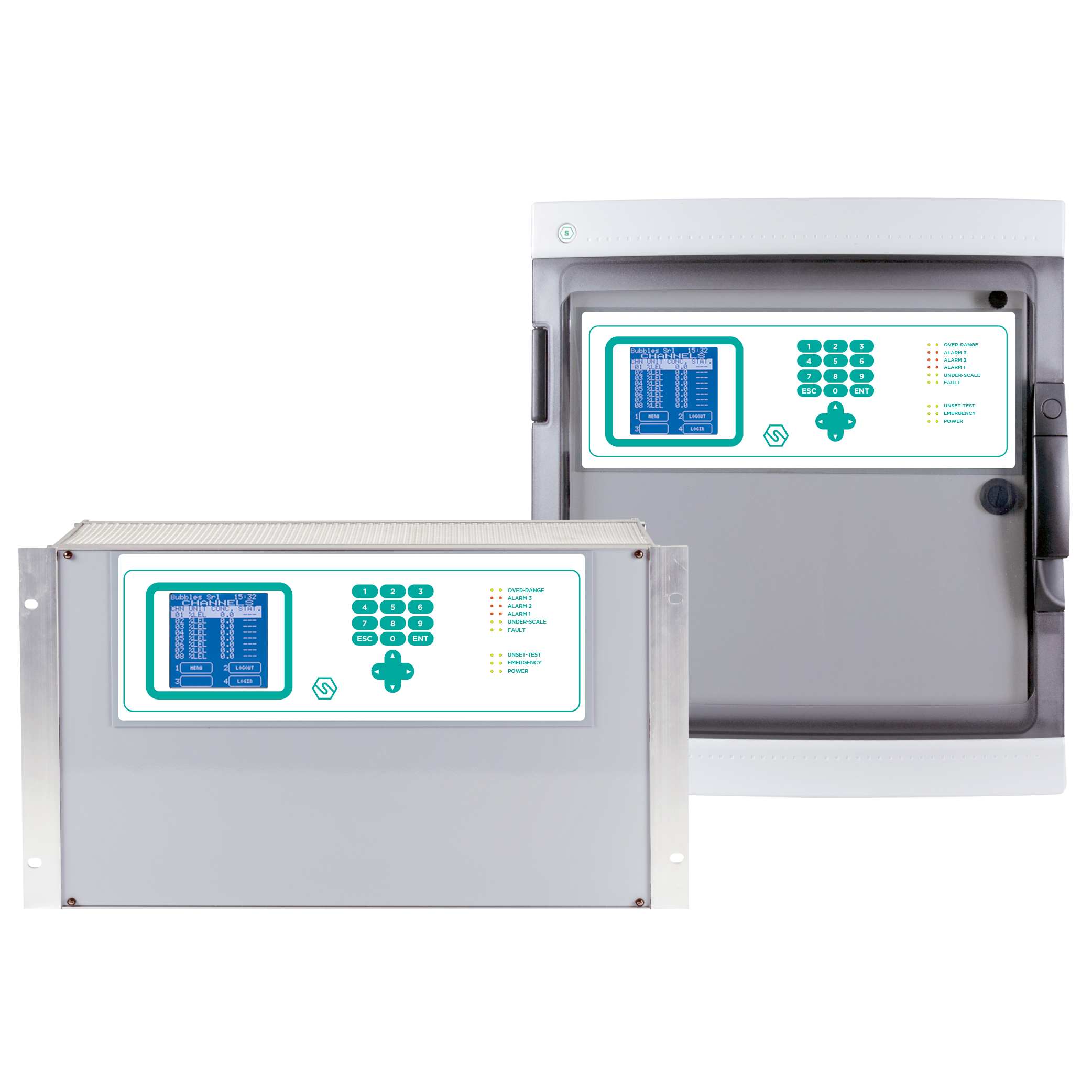
MULTISCAN++ S1/S2
Designed to meet the widest market demand for flexibility, they allow the management of up to 264 detectors. ATEX and SIL certified.