Ammonia (NH3) was one of the first refrigerants used and is still found in industrial refrigeration systems today. Despite the advent of synthetic refrigerants, ammonia remains a preferred choice for many applications due to its excellent thermodynamic properties and environmental benefits.
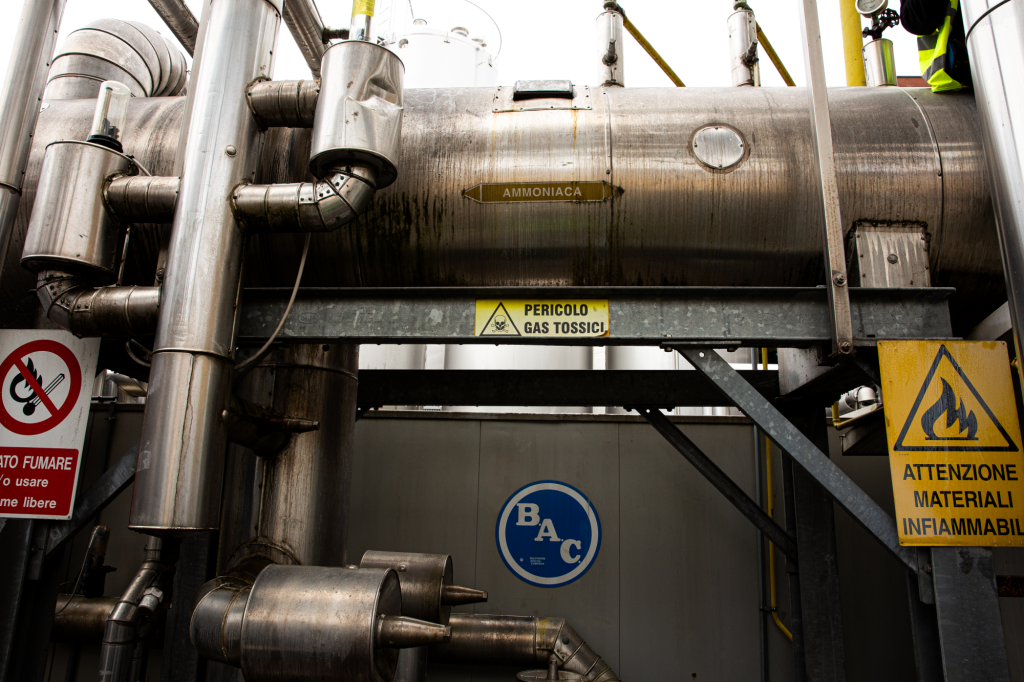
Ammonia: advantages and benefits
Energy Efficiency: ammonia has a high heat capacity and better heat transfer efficiency than many synthetic refrigerants. This translates into reduced energy consumption for refrigeration systems, which is crucial for industries operating in continuous cycles such as the food and chemical industries.
Environmental Impact: Ammonia is a natural refrigerant with zero global warming potential (GWP) and zero ozone depletion potential (ODP). Unlike chlorofluorocarbon (CFC) and hydrofluorocarbon (HFC) refrigerants, ammonia does not contribute to climate change or ozone depletion.
Cost: Ammonia is relatively cheap to produce and is not subject to the same price fluctuations as synthetic refrigerants. Moreover, the superior energy efficiency of ammonia-using plants results in significant savings in long-term operating costs.
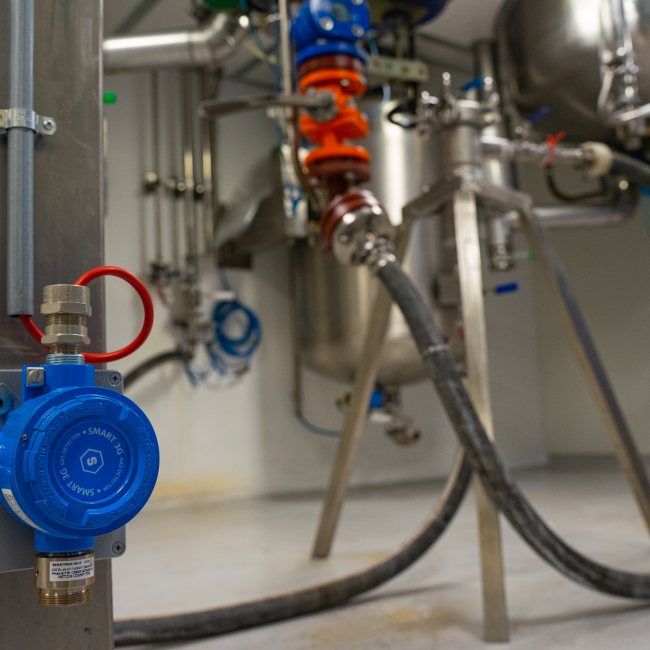
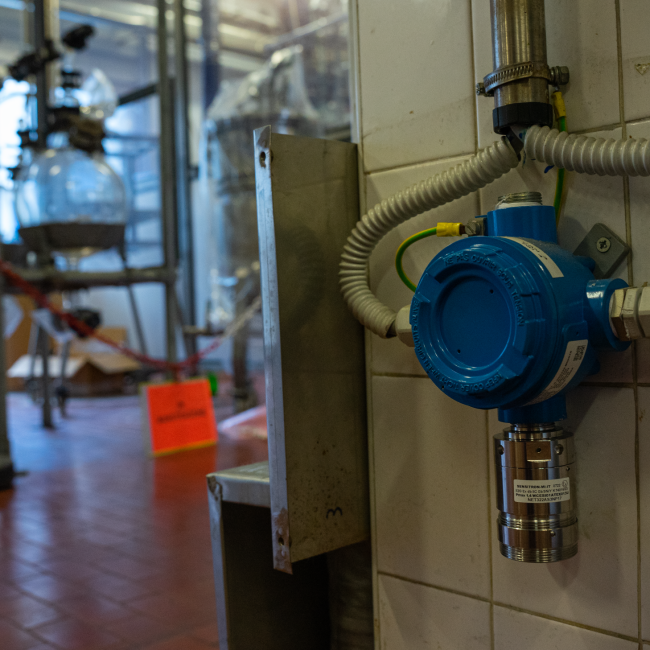
Ammonia: main uses
Ammonia is widely used in various industries, including:
- Food industry: it is essential for the refrigeration and freezing of food, ensuring the preservation and safety of perishable products.
- Ice Production: it is used in ice production plants for commercial and industrial uses.
- Chemical Industry: It is used in critical cooling processes in the chemical and petrochemical industries.
- Air-conditioning plants: Ammonia is also used in large centralised air-conditioning plants, especially in industrial facilities.
Ammonia: the risks associated with its use
There are several aspects of ammonia to which attention must be paid:
- Toxicity and Safety: One of the main disadvantages of ammonia is its toxicity. Exposure to high concentrations of ammonia can be dangerous to human health, necessitating strict safety measures. However, modern plants are designed with leak detection and control systems that minimise the risk of exposure.
- Corrosivity: Ammonia can be corrosive to some metallic materials, particularly copper and its alloys. Plants must therefore be constructed of corrosion-resistant materials such as stainless steel.
- Stringent Regulations: The use of ammonia is regulated by stringent regulations that vary from country to country. Companies must comply with these regulations, which may include specific design requirements, regular inspections and staff training.
Discover our produtcs
Sensitron gas detectors are suitable for use in any application:
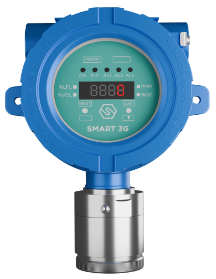
SMART 3G D2
Suitable for detecting flammable substances, toxic gases, refrigerants and oxygen in classified areas.ATEX, IECEx and SIL2/3 certified.
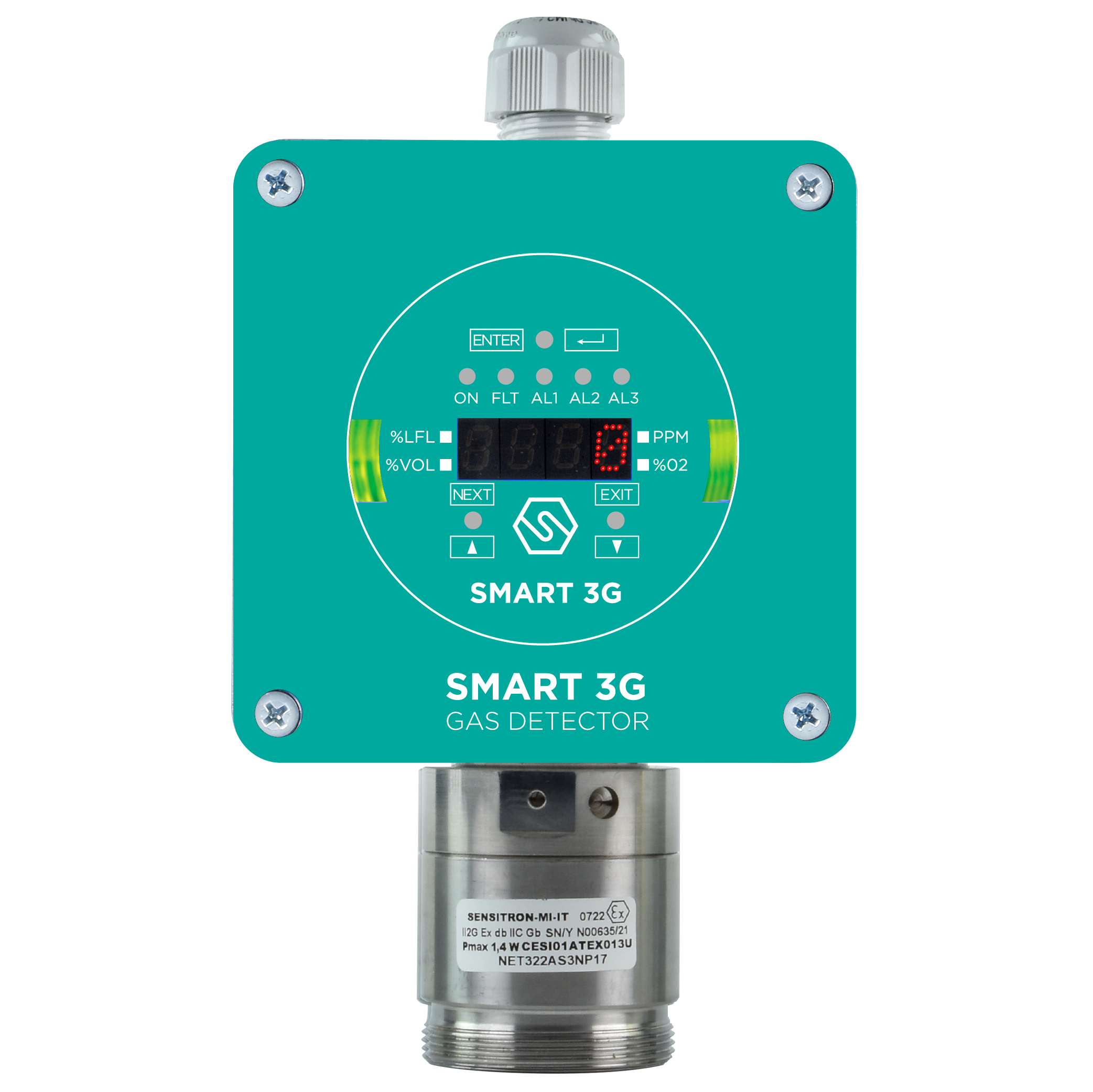
SMART 3G D3
Suitable for gas detection in classified areas, ATEX, IECEx and SIL2/3 certified, allows for non-intrusive field calibration.
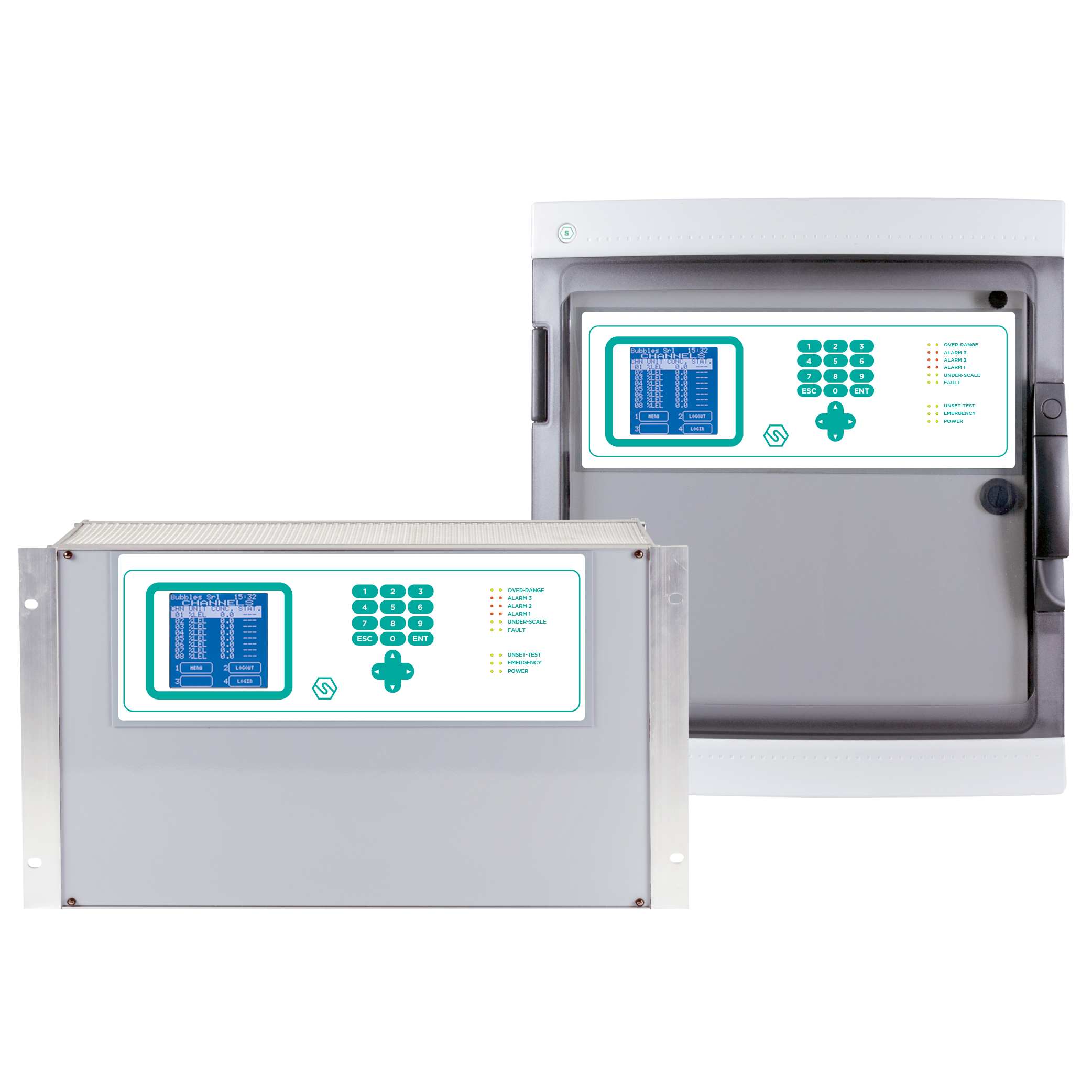
MULTISCAN++ S1/S2
Designed to meet the widest market demand for flexibility, they allow the management of up to 264 detectors. ATEX and SIL certified.
Our certifications
Ammonia can be used in hazardous environments where strict safety standards must be met, which is why all our products are certified and in line with regulations.
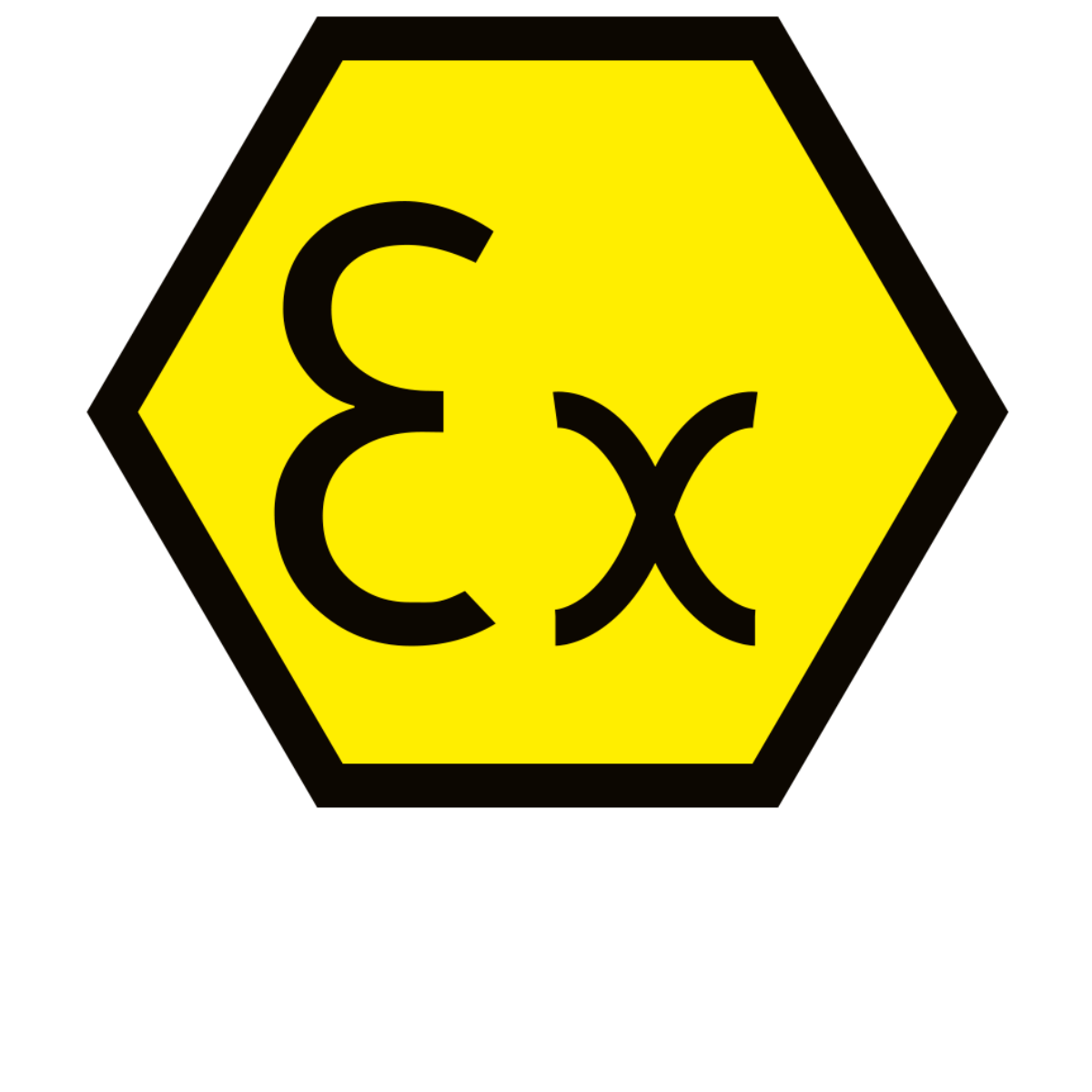
ATEX
The Directive sets out the requirements and assessment of equipment intended for use in potentially explosive atmospheres.
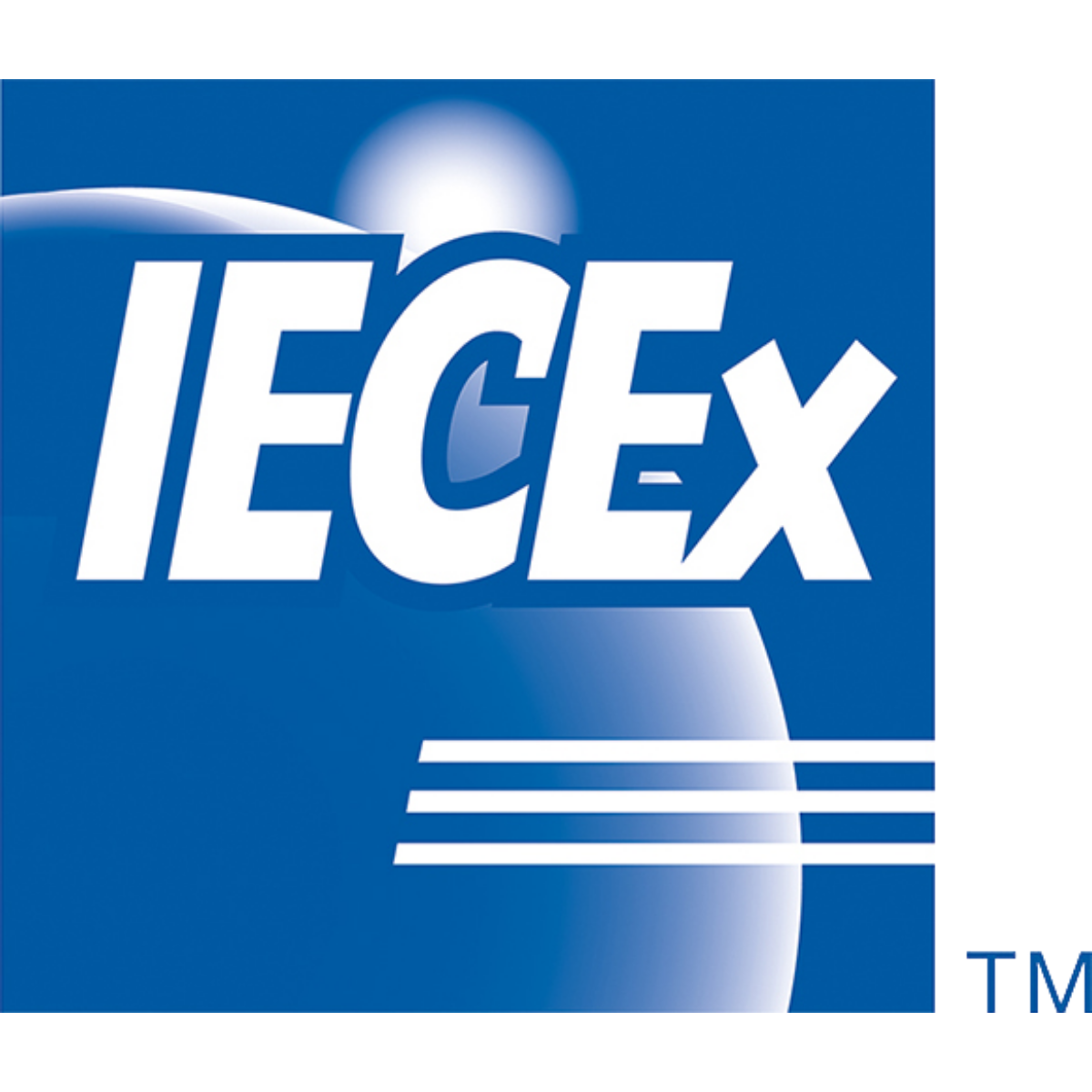
IECEx
The IECEx system is an international certification system. It is developed by the International Electrotechnical Commission.
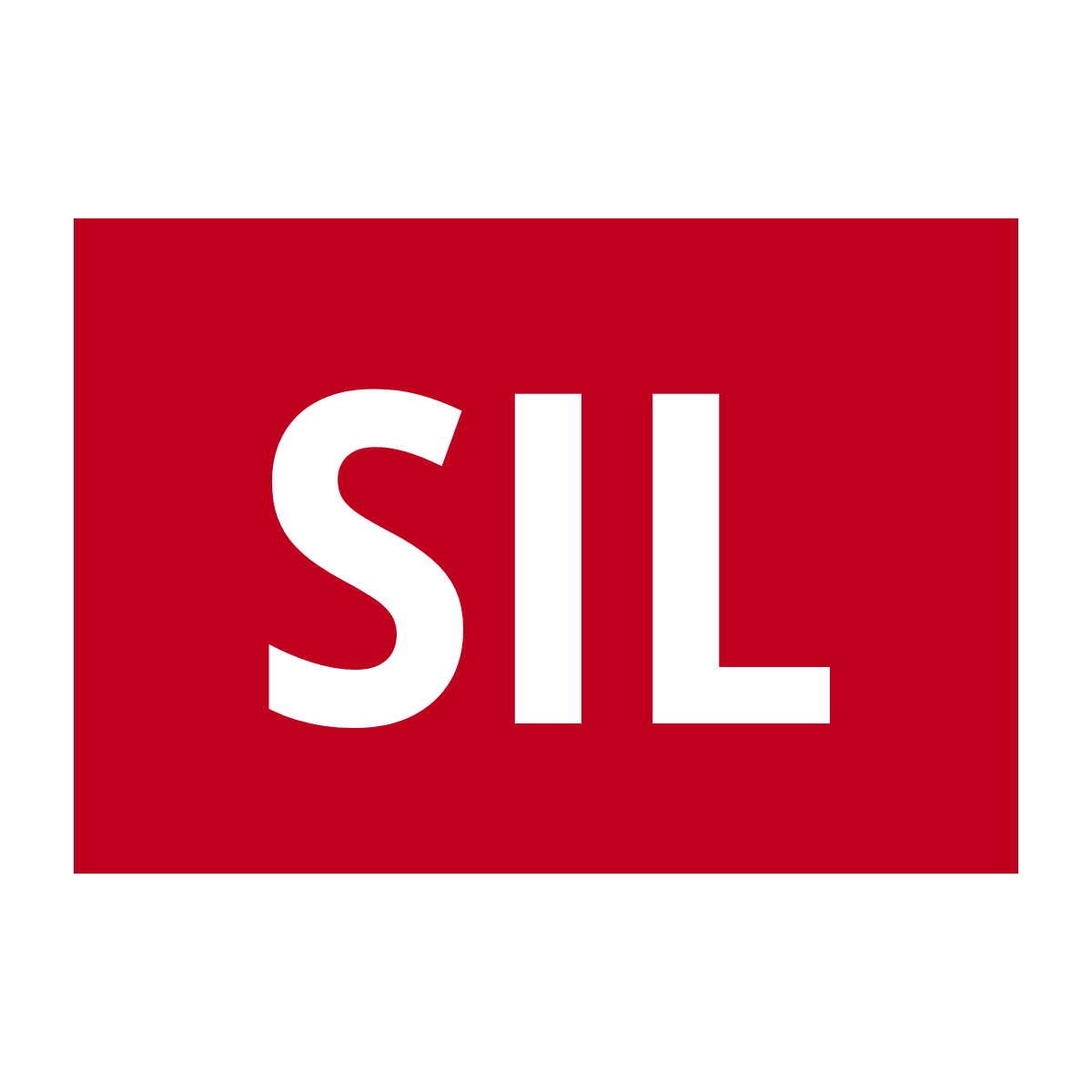
SIL
The Safety Integrity Level (SIL) is the ability to reduce the assessed risk by ensuring the reliability of safety systems.