
ATEX: explosive atmospheres and gas detection
In industrial environments, safety is a top priority, especially when operating in explosion-prone locations. ATEX legislation was created to ensure that protective equipment and systems are suitable for use in potentially explosive atmospheres. Through a series of European directives, ATEX governs both the technical requirements for products and the safety measures employers must take to protect workers. Knowledge and proper application of these regulations are essential to reducing risks and ensuring a safe working environment.
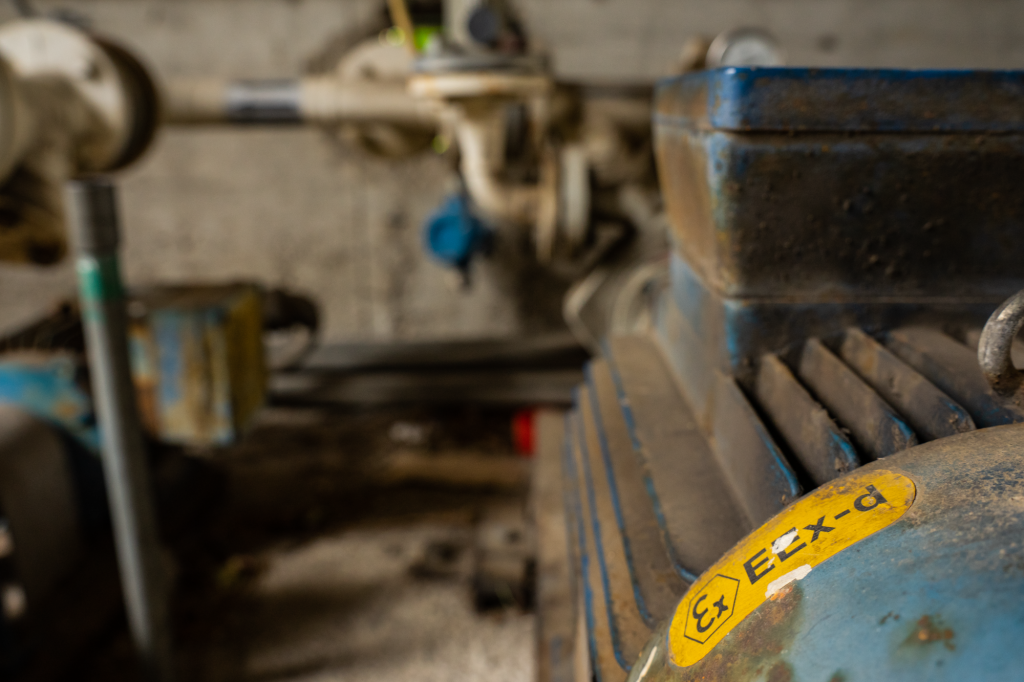
ATEX: historical overview
The earliest forms of regulation specific to explosive atmospheres date back to the early 1900s, when accidents in mines and factories demonstrated the urgency of implementing more stringent safety measures. The most devastating accidents, such as gas explosions in mines, prompted governments and industries to develop standards for equipment used in explosive environments. Later, in the 1960s and 1970s, as industrial technologies and globalization became more complex, it became clear that a more unified approach was needed to manage the risks associated with explosive atmospheres. National standards were not enough, and industry required harmonized standards at the international or continental level.
ATEX: the first directive
The real breakthrough came in 1994, when the European Union introduced the first ATEX Directive 94/9/EC, which defined requirements for equipment intended for use in explosive atmospheres. This directive obligated manufacturers to meet specific design and certification criteria. In 1999, ATEX Directive 1999/92/EC completed the regulatory framework, imposing obligations on employers to ensure the safety of workers. Finally, in 2014, Directive 94/9/EC was replaced by Directive 2014/34/EU, which simplified and updated the previous provisions to take into account technological advances and improve overall safety. Today, ATEX regulations are considered an essential pillar for the prevention of industrial accidents in Europe and are a worldwide benchmark for the management of explosive atmospheres.
ATEX: how it is divided
The term “ATEX” comes from the French words “ATmosphères EXplosibles” and refers to two key directives issued by the European Union:
- Directive 2014/34/EU (formerly Directive 94/9/EC): Regulates requirements for equipment and protective systems intended for use in explosive atmospheres. This directive applies to manufacturers of electrical and non-electrical equipment, who must ensure that their products meet specific safety standards before they are placed on the market.
- Directive 1999/92/EC (ATEX Workplace Directive): Addresses employers and covers the protection of the health and safety of workers working in explosive environments. This directive requires employers to assess the risks associated with explosive atmospheres, implement appropriate safety measures, and train employees.

ATEX: what defines a potentially explosive zone
A potentially explosive zone is a mixture of air with flammable substances (gases, vapors, mists or dusts) that, under certain conditions, can ignite and cause an explosion. Environments such as oil refineries, chemical plants, mills or silos can present this type of hazard. To best manage them, areas with explosive atmospheres are classified into zones:
Flammable gas and steam zones:
- Zone 0: Area where an explosive atmosphere is present for prolonged periods or frequently.
- Zone 1: Area where an explosive atmosphere is likely to occur occasionally during normal operations.
- Zone 2: An area where an explosive atmosphere is unlikely to occur during normal operations but, if it does occur, persists only for short periods.
Combustible dust zones:
- Zone 20: Area where an explosive dust atmosphere is present for prolonged periods or frequently.
- Zone 21: Area where an explosive dust atmosphere is likely to occur during normal operations.
- Zone 22: An area where an explosive dust atmosphere is unlikely to occur during normal operations but, if it does occur, persists only for short periods.
Discover our ATEX certified products

SMART 3G D2
Suitable for detecting flammable substances, toxic gases, refrigerants and oxygen in classified areas.
Certified ATEX Category 2 for Zone 1, IECEx and SIL2/3
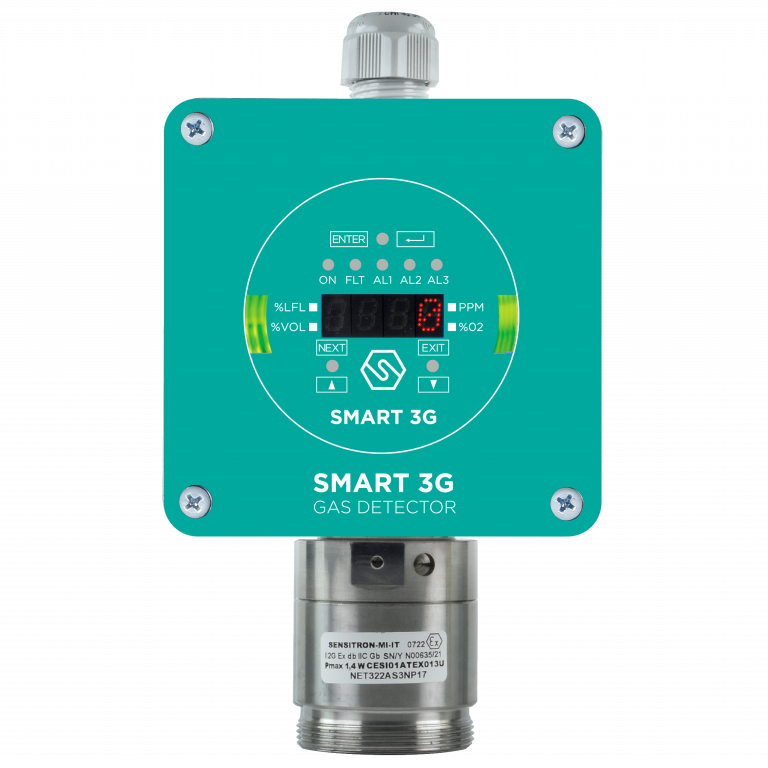
SMART 3G D3
Suitable for detecting in classified areas, Certified ATEX Category 2 for Zone 1, IECEx and SIL2/3, allows non-intrusive field calibration.
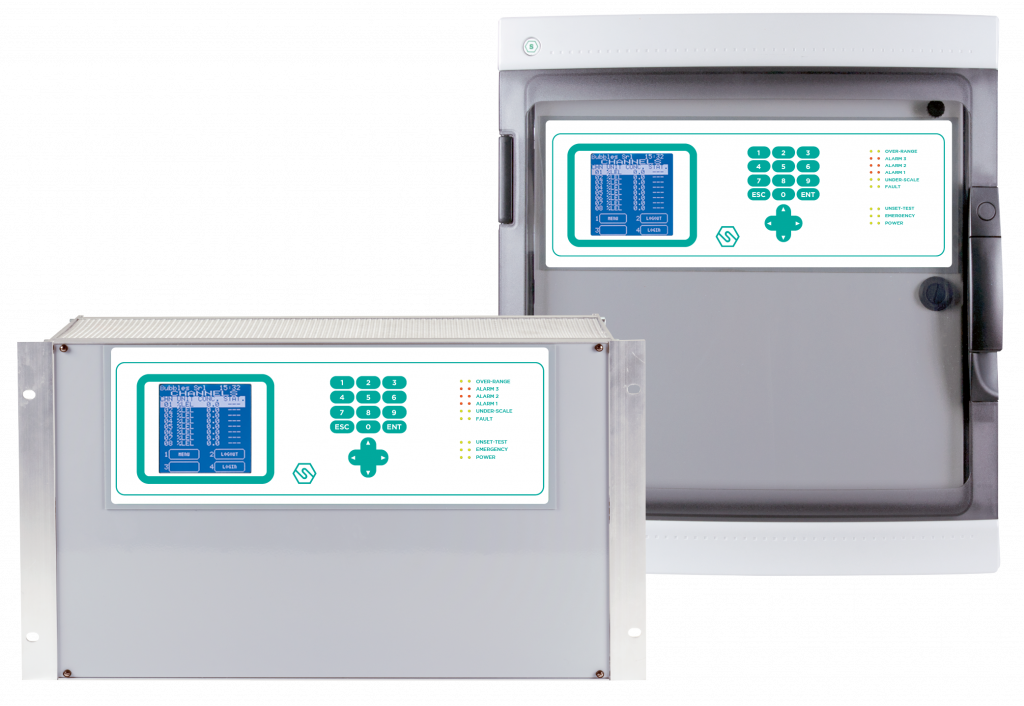
MULTISCAN ++S1/++S2
Designed to meet the widest demand from the market, they allow management of up to 264 detectors. ATEX and SIL certified.
Explore our spaces in virtual reality
Within the Sensitron metaverse you can explore application realities reconstructed in virtual reality. Find out more about who we are and what we do, walk inside a production area and learn more about the dangers of gas.