In highly specialised industrial environments, such as pharmaceuticals, electronics and biomedicals, air quality is a critical factor. Clean rooms and sterile environments must guarantee extremely clean conditions, avoiding the presence of contaminants that could compromise production or personnel safety. Among the various risk factors, the presence of harmful gases is a major challenge. Effective and timely monitoring is essential to prevent anomalies, guarantee regulatory compliance and ensure the integrity of production processes.
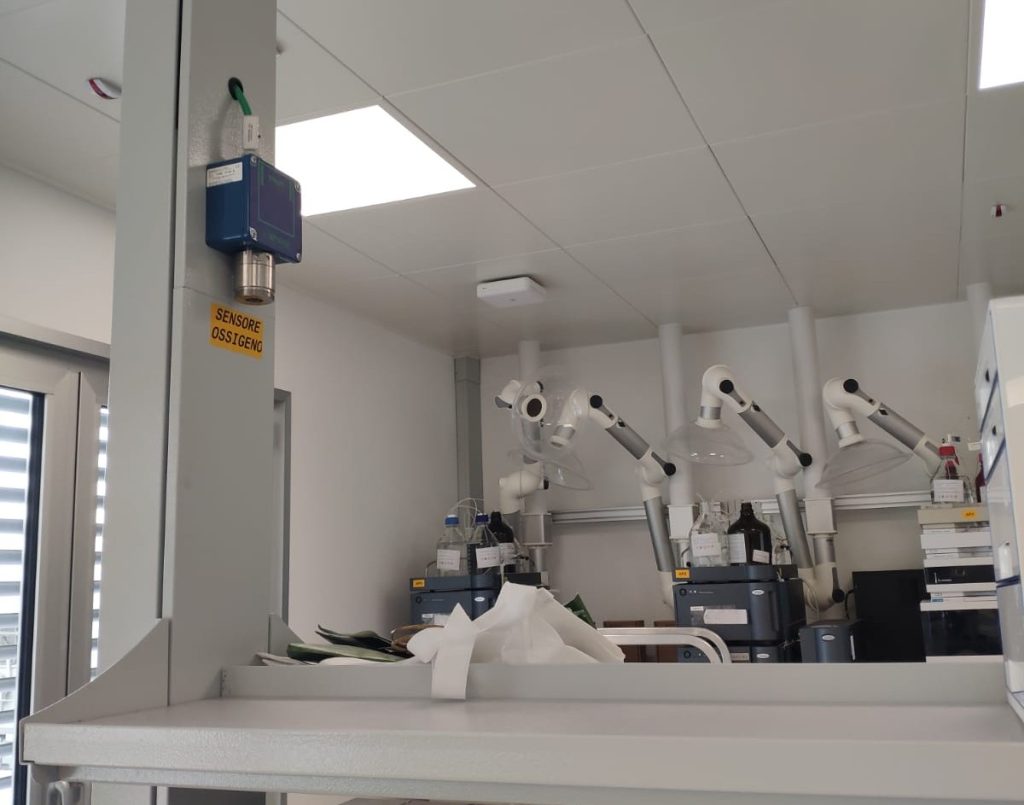
Cleanrooms and gas detection: why it is important
Cleanrooms are designed to maintain controlled contamination levels, with stringent parameters on particles, microorganisms and gases. Some gases, such as ethylene oxide, ozone, ammonia and volatile organic compounds (VOCs), can alter production processes or pose a safety risk to personnel. Early detection is therefore essential to prevent product damage and ensure regulatory compliance.
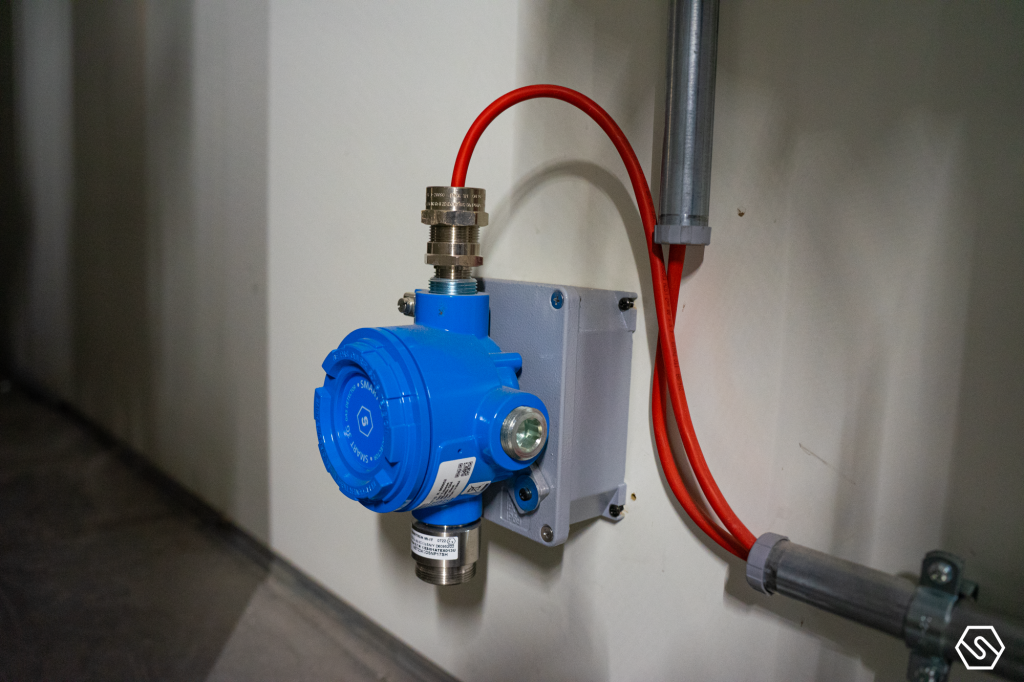
Gas detection in clean rooms: what are the most common gases?
In industrial processes that require clean rooms and sterile environments, several gases can pose a risk. Among the most common are:
- Ethylene oxide (EtO): used for sterilising medical equipment, it is highly toxic and requires constant monitoring.
- Ammonia (NH₃): found in some chemical processes and pharmaceutical industries, it can be irritating and harmful if inhaled.
- Volatile Organic Compounds (VOCs): derived from solvents, adhesives and manufacturing processes, can impair air quality.
- Carbon monoxide (CO): produced by combustion processes, it is highly toxic and difficult to detect without specific instruments.
- Carbon dioxide (CO₂): although non-toxic at low concentrations, it can alter indoor air balance.
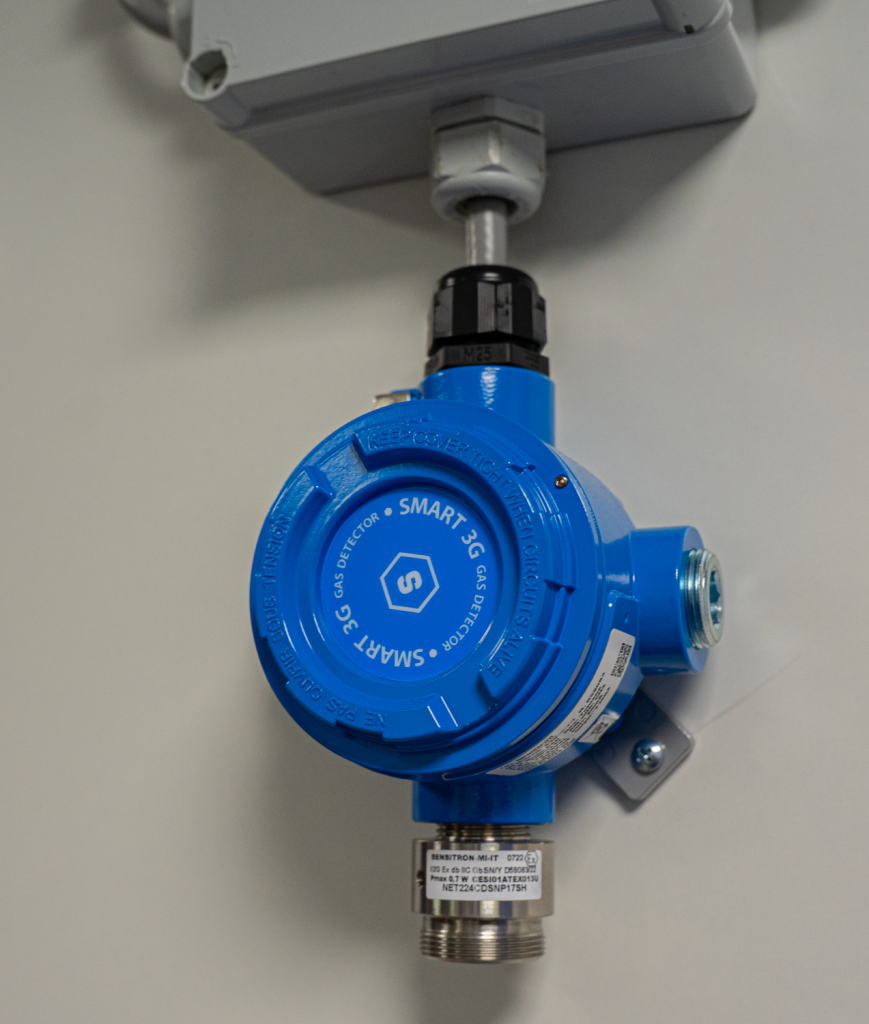
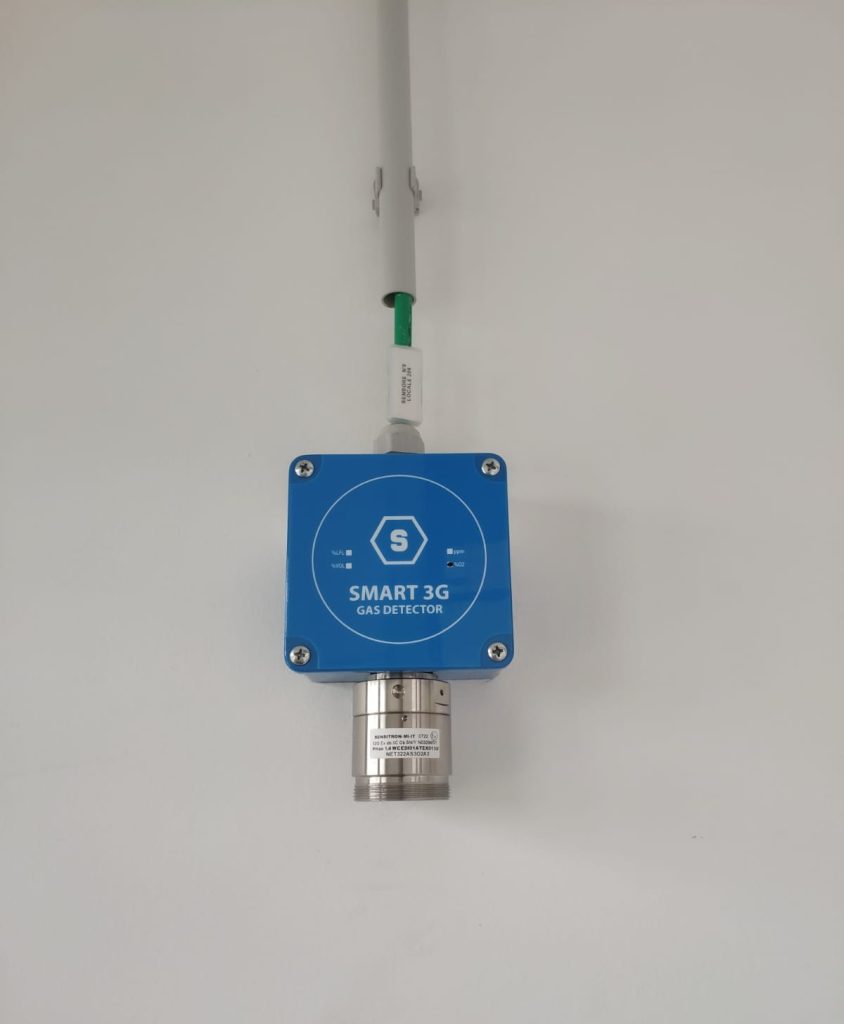
Gas detection technologies in clean rooms
Gas detection solutions for sterile environments must guarantee accuracy, reliability and compatibility with operating conditions. Among the main technologies adopted are:
- Infrared (IR) sensors: ideal for detecting gases such as carbon dioxide and hydrocarbons, without interference from moisture or particulates.
- Electrochemical sensors: effective for toxic gases such as nitrogen oxide, carbon monoxide and ammonia, with high sensitivity.
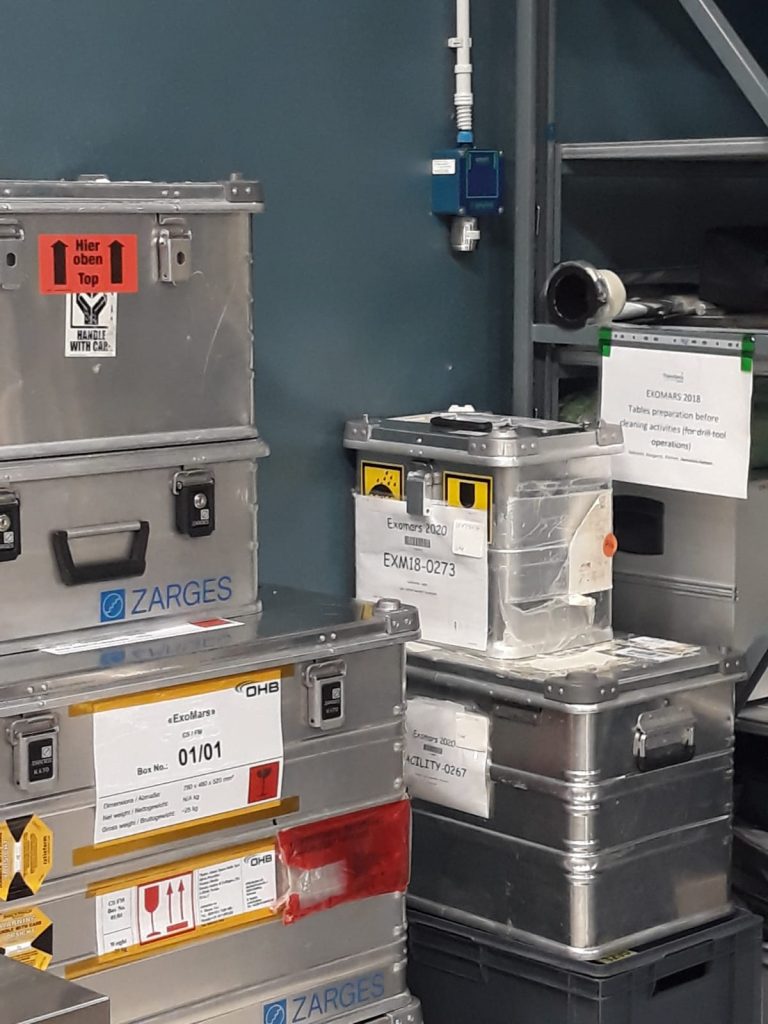
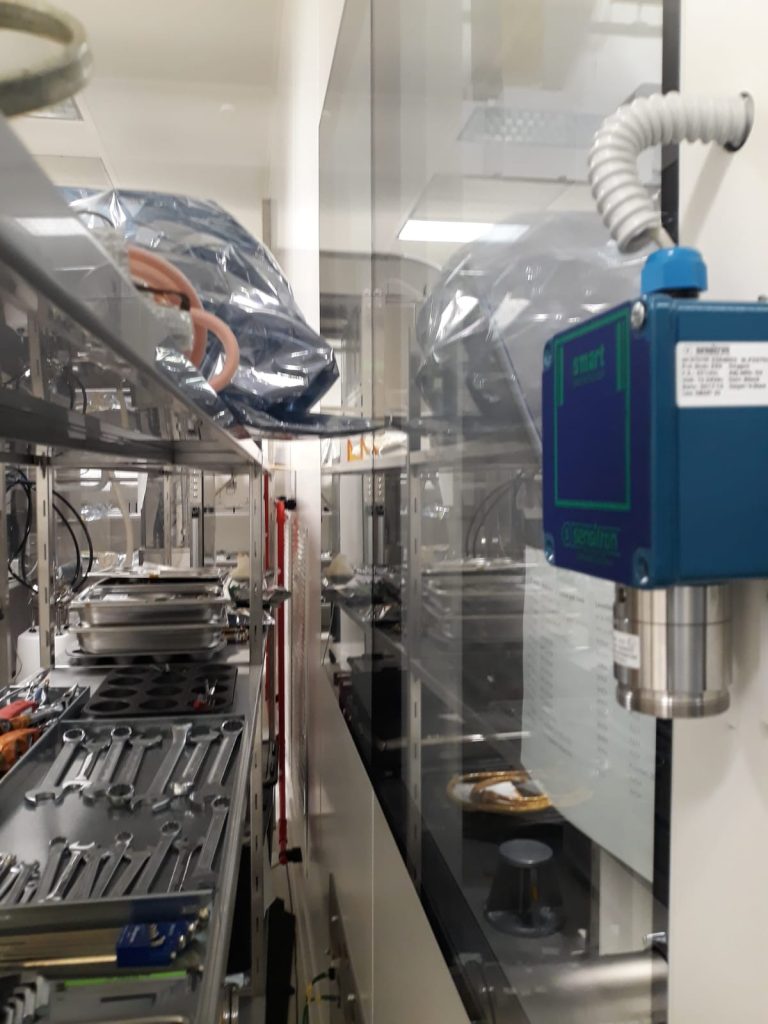
Gas detection in clean rooms: what is important to remember
In addition to choosing the most suitable technology, it is crucial to adopt best practices to ensure the effectiveness of gas detection systems:
- Continuous Monitoring: Implement real-time detection systems to ensure immediate response to gas leaks.
- Regular Maintenance and Calibration: Sensors must be regularly calibrated to ensure maximum accuracy.
- Integration with Automation Systems: Connect detectors to environmental management systems to trigger alarms or automatic intervention.
- Staff training: Staff should be trained in safety procedures and handling of gas-related emergencies.
- Regulatory Compliance: Follow international and local guidelines for cleanroom safety, such as ISO for cleanrooms and ATEX directives for hazardous areas.
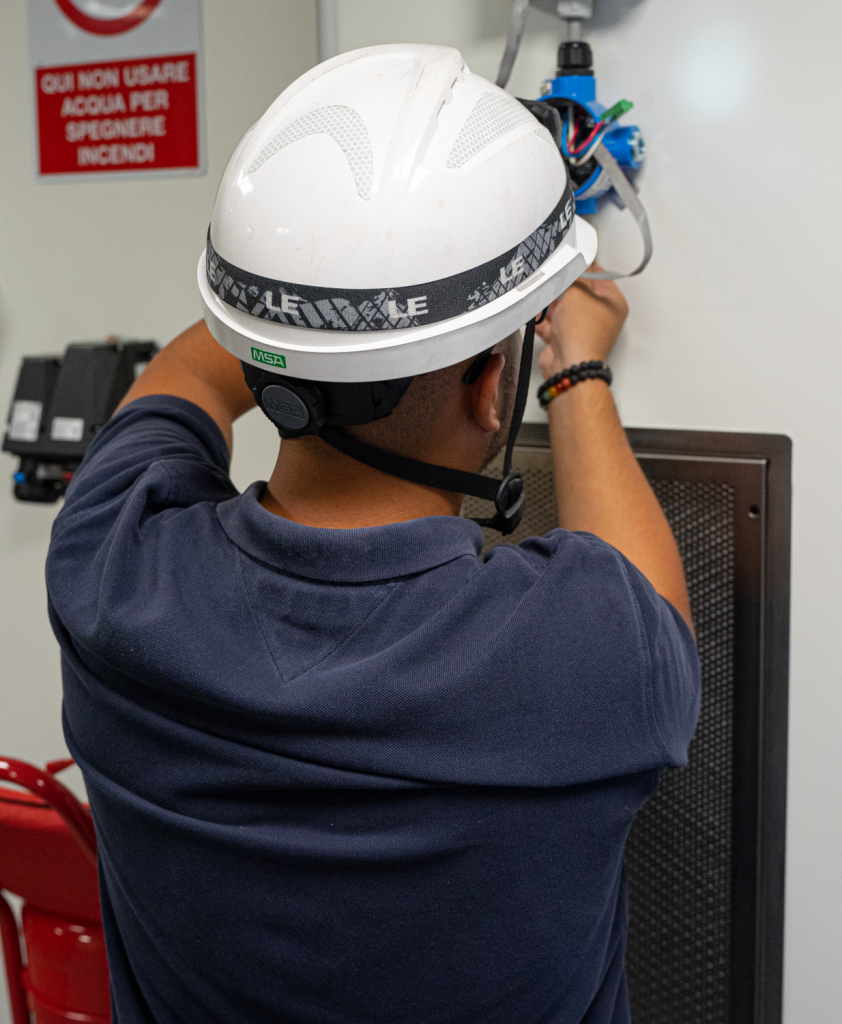
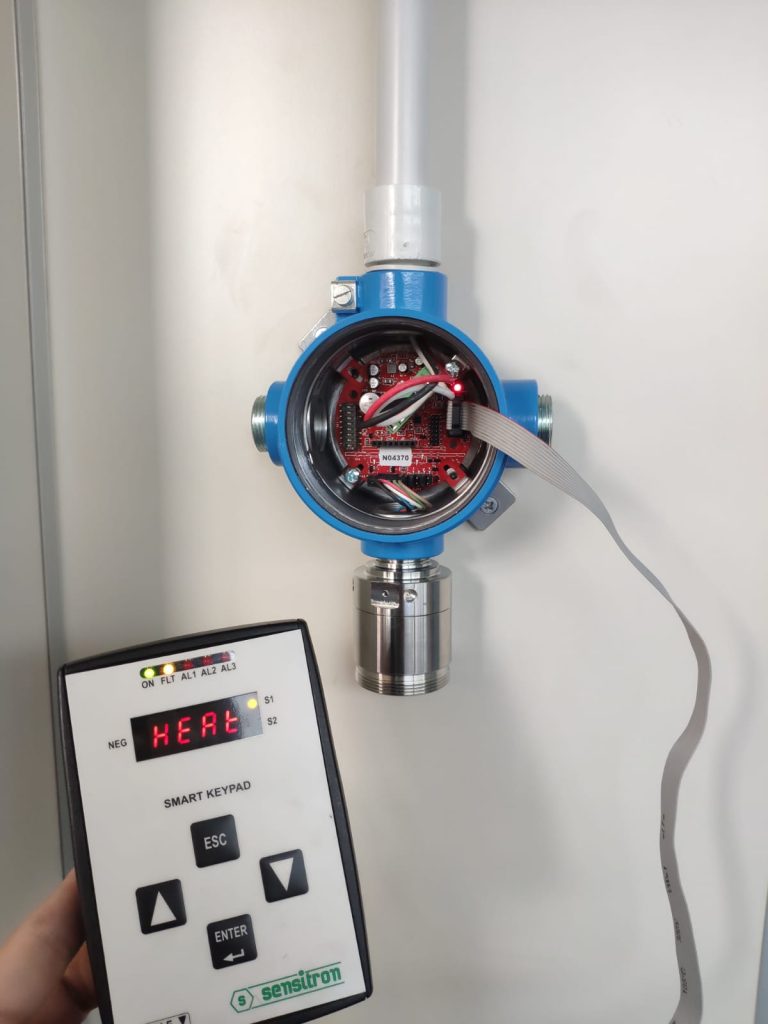
Our products for Clean rooms
Sensitron gas detection systems are suitable for use in clean rooms or clean rooms, these are some of the possible solutions.
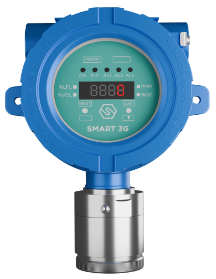
SMART 3G D2
Suitable for detecting flammable substances, toxic gases, refrigerants and oxygen in classified areas.ATEX, IECEx and SIL2/3 certified.
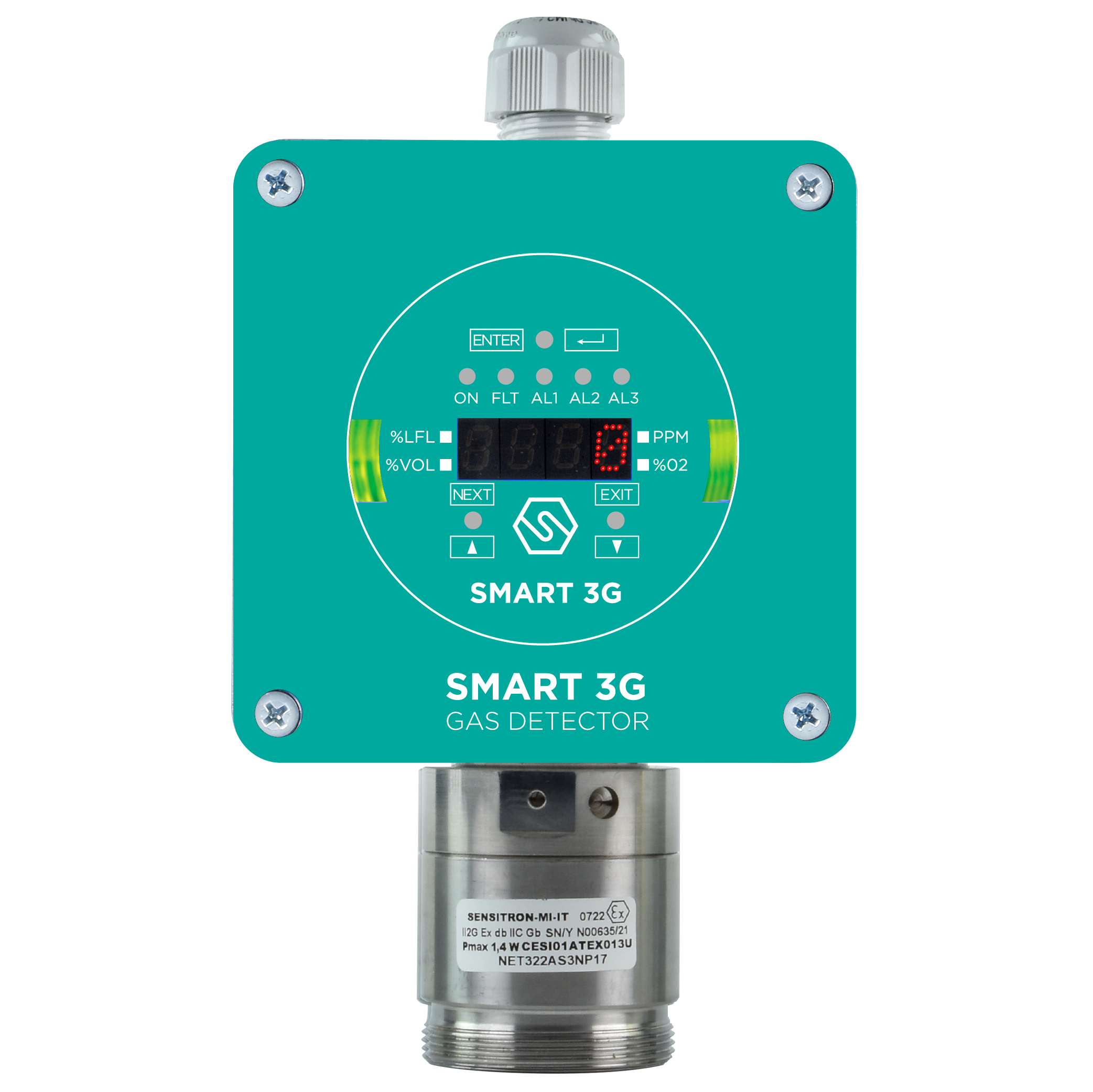
SMART 3G D3
Suitable for gas detection in classified areas, ATEX, IECEx and SIL2/3 certified, allows for non-intrusive field calibration.
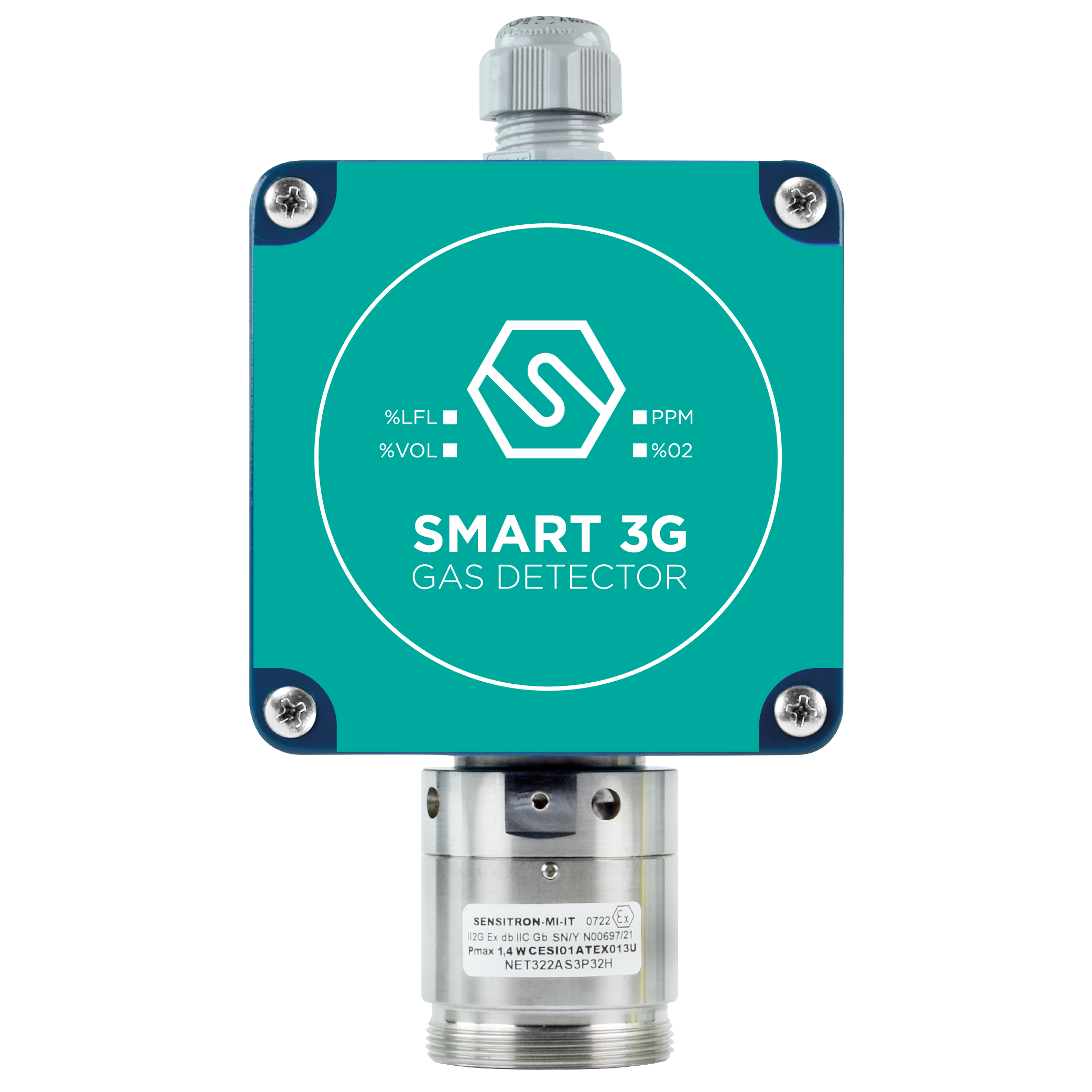
SMART 3G C3
Suitable for gas detection in classified areas, ATEX, IECEx and SIL2/3 certified, allows for non-intrusive field calibration.